Eliminate dependency on manual labour and/or third party suppliers
A MID-SIZE PMGSY/ PWD ROAD CONTRACTOR WAS UNDERTAKING A 45 KM ROAD IN THE NORTHERN PART OF INDIA
Until now, they were constructing road by breaking the hill with the help of manual labour. They used to deploy approximately 60 daily labourers for the said purpose. The manual labours were preparing for G1 (63mm down), G2 (50mm down), G3 (25mm down) and they were sourcing macadam (less than 15mm down) from the local crusher.
But there was lot of inconsistency in the quality of the end result and on productivity.
Are you operating in Low Margin High cost game?
The company was incurring huge cost owing to the manual labour requirements (approximately INR 12 to INR 16 per Cubic foot (CFT)) depending on the required size of the material. Their daily productivity was close to 3 to 4 truckloads (of 400 CFT each) equalling around 1200 to 1600 CFT per day.
In order to maintain pace with the project timelines, they had to purchase aggregates from the local crusher site at a much higher rate and incur huge transportation cost.
They soon realised that this was a high cost and low margin game for them.
Convert your heavy equipment into Crushing and Screening machine directly at site
With the extension of the restrictions in the several parts of India, the contractor started to face labour issues at his site. Finally tired of the inconsistency in the aggregates production and the uncertainty of the labour force re-joining work to complete the project in hand, they started looking for alternative solutions.
Upon contacting MB Crusher, they were advised to continue to excavate the hill rock and segregate the 20mm down requirement with the help of MB Screening Machine MB-S18 S4 which fulfils their 20mm down requirements and with the help of MB Crusher Bucket BF90.3 S4, they can crush the material to meet their G1, G2 and G3 requirements directly at site. With one operator, one excavator and MB Product Crusher and Screening machines, the customer was able to convert the excavator into a Mobile Crushing and Screening machine directly at site.
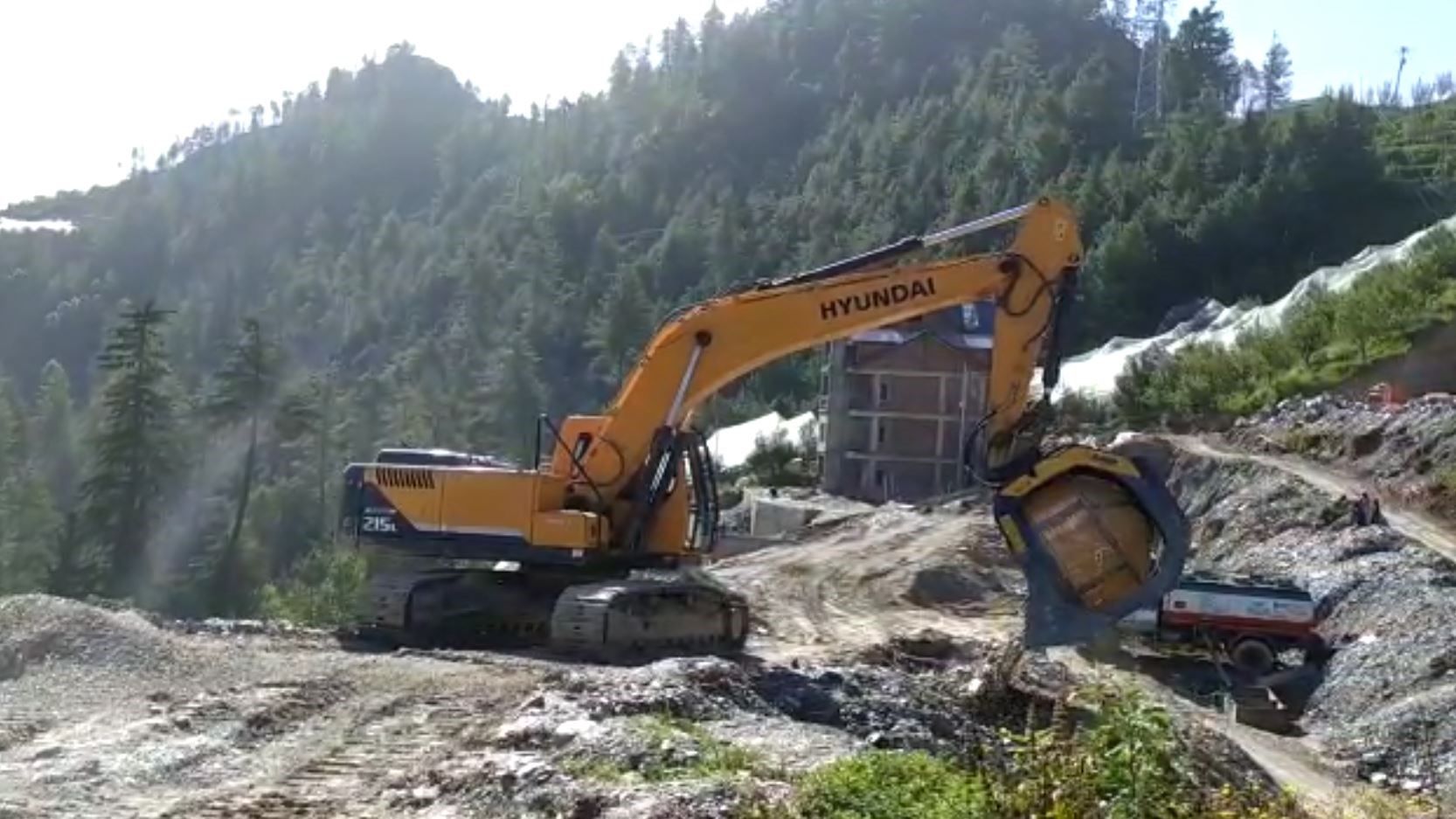
Eliminate dependency on manual labour
This also ensured that the entire operations is automated now with consistent output and their dependency on the manual labour is also eliminated in the most profitable manner. Soon after installing the machines at their construction site, they are now able to achieve the productivity of approximately 500-600 CFT & Per Day, which is equivalent to 10-12 Tipper @400 CFT, totalling around 4000 to 5000 CFT, as per output size.
With MB Crusher products, they were able to meet their aggregate requirements by increasing productivity, they became independent, reduced costs significantly and improved the overall profitability for the company.