The before during and after a coal power plant
BEFORE: THE EXTRACTION
Aim: reduce all unnecessary costs.
With an MB Crusher MB-HDS323 padding bucket and the carrier a Caterpillar 329D at the quarry extraction point, the coal is reduced in size, in one single-step operation.
CHALLENGE 1: DURING THE RAINY SEASON, THE COAL BECOMES WET AND STICKY, MAKING THE CRUSHING PHASE TO FEED THE POWER STATION DIFFICULT.
→ After extraction, in one motion, the MB shaft screener scoops up the damp coal, the rotating shafts reduce down to smaller size the soft, sticky rocks. While been reduced it was also loaded into the truck.
The RM Mixer shaft-mounted is not affected by the dampness nor the stickiness of the wet coal.
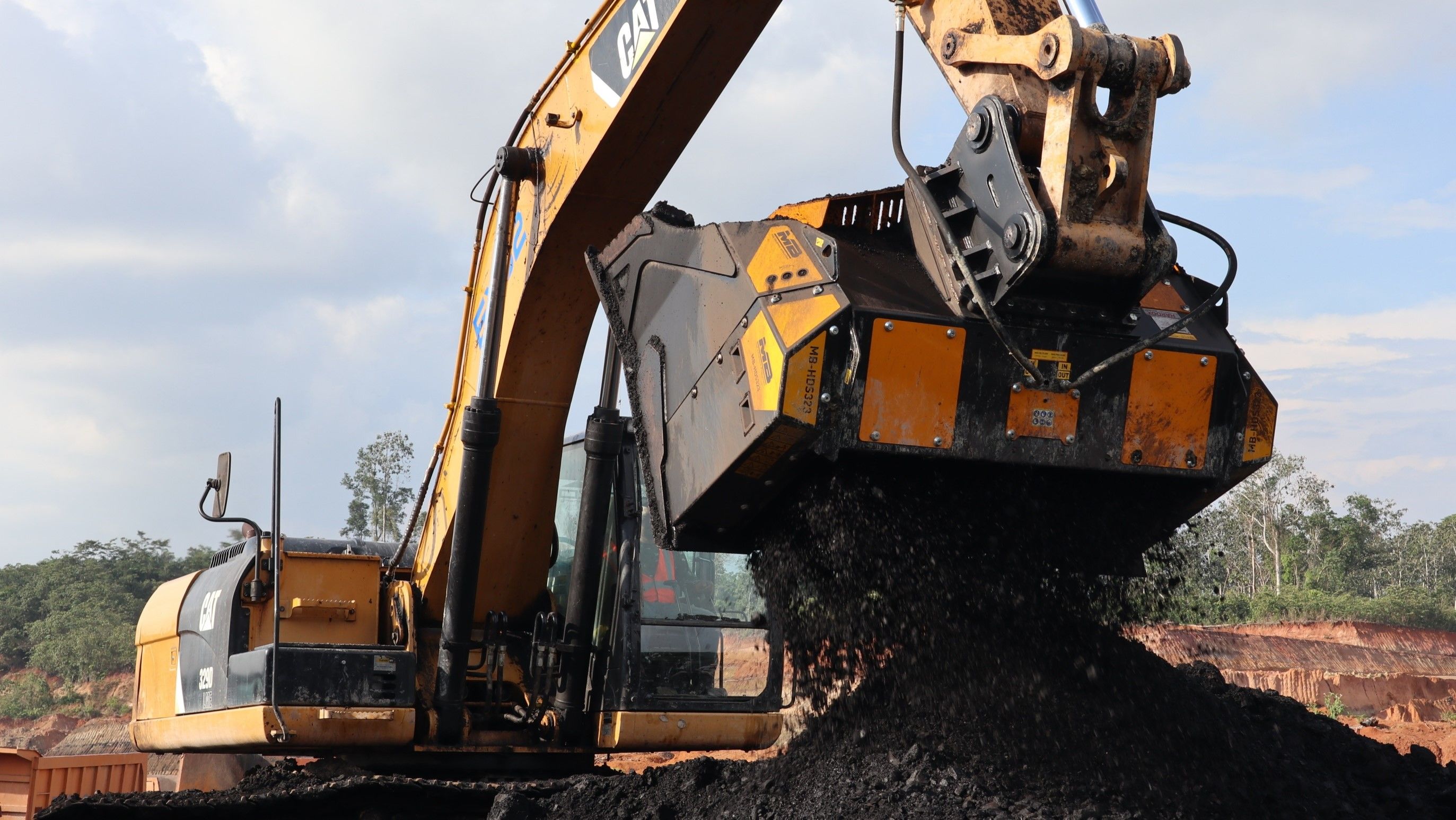
CHALLENGE 2: THE USE OF A CRUSHING PLANT IS COSTLY AS THE COAL NEEDS TO BE HAULED FROM THE EXTRACTION POINT TO THE ACTUAL PROCESSING STAGE AND THEN HAULED AGAIN TO THE POWER PLANT.
-
How to choose:
- the selection is made based on the carrier weight
- different types rotating shafts can be purchased for the same unit
- each of the 6 types of shafts is designed to carry out a specific task
MB’s Advantage:
Eliminate the need to purchase different attachments, just one unit equipped with different rotating shafts is the solution.
DURING: WASHING COAL
Aim: be more sustainable.
With an MB trommel screener MB-S18 and a Hyundai excavator, the coal is washed and impurity removed with a sustainable and cost-effective process.
→ Coal preparation is the first step in the power cycle. The screening bucket rotates inside the water tank, sifting and cleaning at the same time. One unique passage and this sustainable process contributed to reducing operating costs with a 30% improvement to their previous system.
Add new equipment permitted the company to lower the operational costs and be more sustainable. JOB DONE!
HOW TO CHOOSE:
- 4 models for excavators from 4 ton
- 2 models suitable for loaders and skid
- Grid size can be selected based on which job needs doing
MB’s Advantage: the modular panels of the grids can be changed to a different size in a few minutes, so one screener can be equipped with a different set of grids.
AFTER: HAVING A CRUSH
Aim: increase operations.
With an MB jaw crusher BF70.2 mounted on a Kobelco SK200 a huge amount of coal ash is recycled and repurposed.
→ By mechanically crushing the dried residue, they could not meet the needed volumes, but with the MB Crusher unit, they managed to substantially fasten the operation and reduce costs. The BF70.2 has increased the hourly production rate, giving them more product to sell.
CHALLENGE 2: FIND A PRICE-EFFECTIVE, PRACTICAL SOLUTION TO REDUCE TRANSPORT COST.
→ The volume of dusty residue received from the plant is huge and subject to strict regulations. With the MB Crusher bucket, they work directly from the excavator cabin and they crush directly on the truck that will transport the processed material to its destination.
CHALLENGE 3: GET A HIGH-QUALITY PRODUCT READY TO BE RECLAIMED.
→ Thanks to the MB jaw crusher bucket unit they obtain regular graded material. Also as it is possible to adjust the jaws output can they reuse the product as a roadbed and also for the redevelopment of the surrounding rice fields.
Changing the way they operated by adding a new attachment has given this company more product ready to be sold, in a shorter time. JOB DONE!
-
select line based on the type of carrier and its weight
- 4 models suitable for loaders and skid
- Adjust jaws to the desired output, the product obtained is homogenous
MB’s Advantage: All of the units are designed to save on maintenance costs, both in terms of the specialised workshop and machine downtimes. Several centralised greasing systems are visible and they are manufactured to preserve the carrier life.
MB CRUSHER ATTACHMENTS OFFER AN EFFICIENT WAY OF REDUCING COSTS, OPTIMIZE THE USE OF RAW MATERIALS AND ENHANCE OPERATORS SAFETY.
GET IN TOUCH TODAY TO GET ONE.