"Using the crushing bucket has saved us considerable time, as well as transportation and material costs."
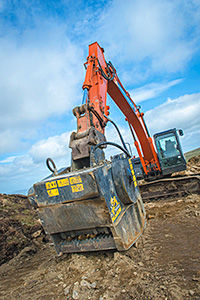
Posted on February, 2014 by Project Plant in Features
MCGOWAN Outdoor Access can now achieve 100% recycling of materials in the Scottish countryside thanks to a MB Dig A Crusher Crushing Bucket, supplied by Worsley Plant.
Since 2009, McGowan has been providing low impact, environmentally sensitive methods of construction to create roads, pathways and bridges in rural Scotland. With the increasing number of outdoor access activities being actively encouraged by the government, coupled with more emphasis being placed on preserving and protecting the natural environment, their aim is to facilitate access for all types of user groups. These groups range from a family taking a country walk in the park to cyclists, runners or horse riders, as well as facilitating sporting events for Scotland's estates and landowners. Their clients include private estates, National Parks, such as Loch Lomond, and government bodies such as the Forestry Commission. In some locations throughout Scotland there is a large amount of Peat Hags with little mineral material. Added to this, accessibility to the site is often difficult which makes the potential to bring in material a lot harder. Utilizing the isolated sources of rock outcrops near some of these sites seemed a good solution to the problem but McGowan needed to find the best way to break these down and make them suitable for use. Ross McGowan, the MD of McGowan Outdoor Access went directly to Worsley Plant and spoke to Sean Heron, their Managing Director. Sean recommended the MB Dig A Crusher BF90.1. Working with this crushing bucket, they were able to crush down the rock to 60mm and then transport it where it was needed in dumpers. The material from these rock outcrops produced a good quality product to use on the job with the added benefit of allowing recycling of naturally available materials. With the roads located high up in the mountains, the location of a larger crushing plant was unfeasible. Using the crushing bucket on a Hitachi Zaxis 210 McGowan have been able to produce 30 tons of material per hour. For just £3 a ton they are then producing a product that once transported onto the job they are then crushing down from 60mm down to dust. Ross has been extremely happy with the product and the service level offered by Worsley Plant and is now considering a MB Dig A Crusher BF60, a smaller crushing bucket, to work on smaller scale jobs such as mountain paths. He said, "Using the crushing bucket has saved us considerable time, as well as transportation and material costs. The nature of our work and the difficult access to many jobs means that recycling materials not only makes the job more cost effective, but also helps us to achieve our aim to provide environmentally friendly methods of building roads, pathways and bridges in rural areas thus protecting the natural environment and reducing our carbon footprint."