RAW MATERIAL SCARCITY
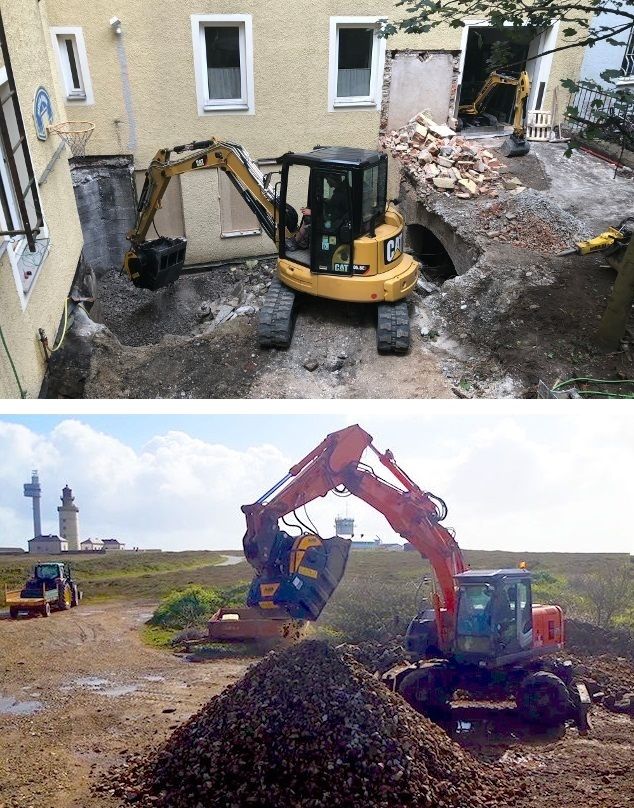
Construction logistics and ordering costs
Efficient planning of materials procurement and storage used to be an important task directly linked to project profitability. Inland companies had the luxury of:
- order smaller quantities of material;
- order more frequently;
- minimizes the locked-up capital in material inventories;
However, it is no longer the case: this modus operandi in the current situation will simply mean material shortages and project delays.
While companies that are working in an island have to face firstly a critical stage of planning and then have to:
- order larger quantities of material as they need to be imported from overseas producers;
- pay higher transportation rates;
- wait longer for the delivery;
- face storage concerns;
- have a huge sum of capital is locked- up in inventory.
Lately, most foreign and domestic manufacturers of construction materials stopped or slowed production because of the pandemic restriction, the lack of production is turning into material shortages or rationing.
Importing construction materials in this time of shortage can quickly translate into construction delays.
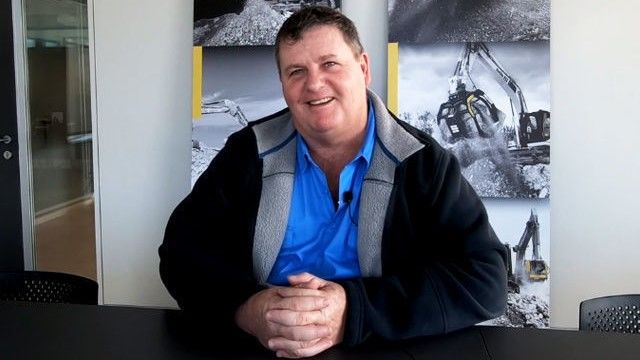
Other aspects that have changed in the last few months are:
- the price rise in building materials supplies;
- the inability of suppliers to export to desired locations;
- the stoppage of imports.
It is time for construction contractors to start looking for alternate supply, to avoid supply hiccups, and the rush to procure supplies. Building construction firms should start looking for alternatives,right now.
Ushant Island, France a jaw crusher BF70.2 and MB-S14 screening bucket and began manufacturing recycled aggregated from debris
With the price to bring in material from the continent going up, this public works company found the solution to reduce the bill while preserving the environment.
By recovering demolition rubble they are saving on procurement money and also addressing a crucial issue: old quarries are now saturated consequently waste storage is tight.
With the MB’s mobile crusher and screener Jean-Jacques Perhirin company has:
- saved natural resources;
- avoid the costs of importing aggregated by sea;
- be able to work in narrow spaces.
They are now utterly able to make their aggregates, by sifting rubbles to separate the smallest portion and then reducing the bigger pieces with the jaw crusher. Et voilà hardcore, for paving, foundation and fillings are ready in no time.
Key message
Any excavator, loader or skid steer, can be equipped with an MB Crusher attachment and began to produce aggregates. The price for the job will decrease, you will not face any delivery delays, and you can use all the stockpile laying around without having to face landfill costs.
Nowadays being independent is a must for construction companies to be able to finish a job on time.